ベアリング故障の原因分析は名探偵の仕事
以前のコラムでもご紹介した通り、ベアリングはいつか必ず壊れます。壊れ方も使用条件や環境により千差万別です。故障の原因分析はこれまでに積み重ねた知見から、類似した現象や状態を探し出し、共通項を見つけたのちに推定することで行います。
一言でいうと簡単に聞こえますが、これがなかなか難しい作業であり、積み重ねた経験がものを言う作業となります。
また、ベアリングの知識だけではなく、ベアリングを組み込んでいる機器についての周辺知識も持ち合わせていないと、誤った原因推定を行い真の原因にたどり着けないことがあります。当社はベアリングメーカーとして、お客様からベアリングの調査依頼をお受けし、ベアリングをお預かりして調査を行う機会が多くあります。ここでベアリングメーカーの頭を悩ませることは、ベアリング周辺の情報が無い、または少ない場合です。
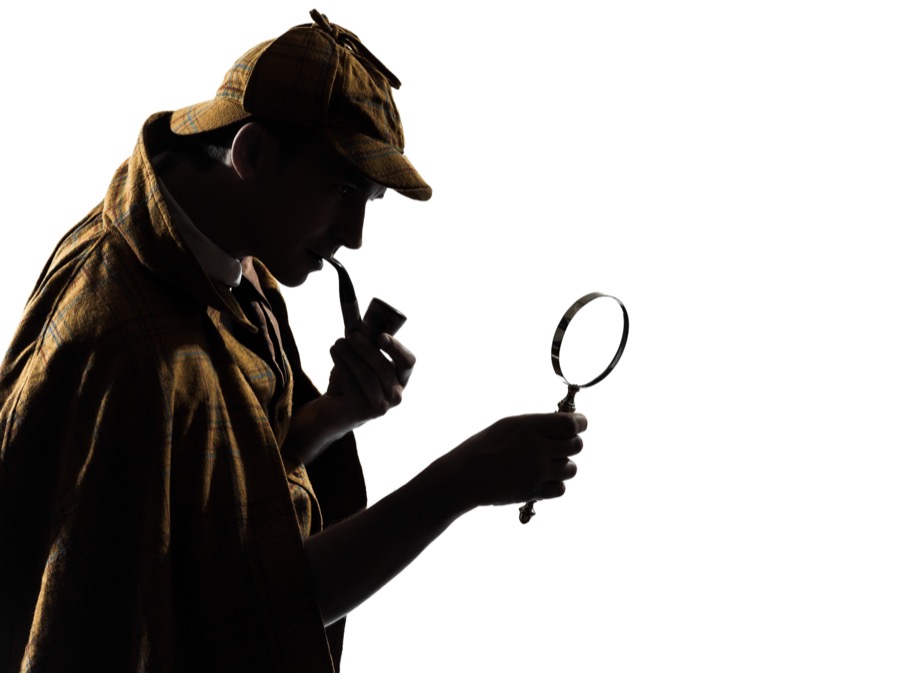
起こりがちなパターンとして、完全に破損してしまったベアリング部品(例えば、真っ黒に焦げてしまいバラバラになった外輪・内輪・鋼球)から、壊れた原因を調査して欲しいというような場合です。例えると、割れた花瓶だけを見て犯人を特定する、シャーロックホームズ並みの推理が要求されます。
シャーロックホームズであっても、室内に残された痕跡など周辺の情報が無いと、トリックの解明は恐らく難しいでしょう。「室内に残された痕跡」にあたる情報が、ベアリングの周辺情報です。
我々は、ベアリングの状態と周辺の情報を照らし合わせながら、機械に起こったであろう状況を想像し、推理を行って故障の原因を探って行きます。さながら、名探偵のようです。
どのようにすれば、故障の原因分析がしやすいのか?
ベアリングが故障した真の原因に辿り着きやすくするためには、どのようにすれば良いのでしょうか?
本来は、ベアリングの状態と周辺の状況をつぶさにモニターしながら、ベアリングの状態の推移を逐一観察することが最も効果的な方法です。ベアリングの温度や振動、荷重変化などを測定し、測定値に変化が起きた際のベアリングに起こっている現象を把握すれば、どのような状況下でベアリングが壊れたのか一目瞭然となります。(実際に、ベアリング単品で耐久試験を行う場合は、上記のような方法でベアリングの状態を確認しながら試験を行います)
ただ、実際の製品に組み込んで運転をしている場合は、このようにベアリングの状態を観察することは難しいと思います。そういった場合には、まずは故障したベアリングの周辺状況をよく観察することから始めることをおすすめします。「壊れたベアリングを取り外して確認したい」という気持ちは良くわかりますが、ひとまず冷静になり、取り外す前に周辺から集められる情報をできる限り集めてください。
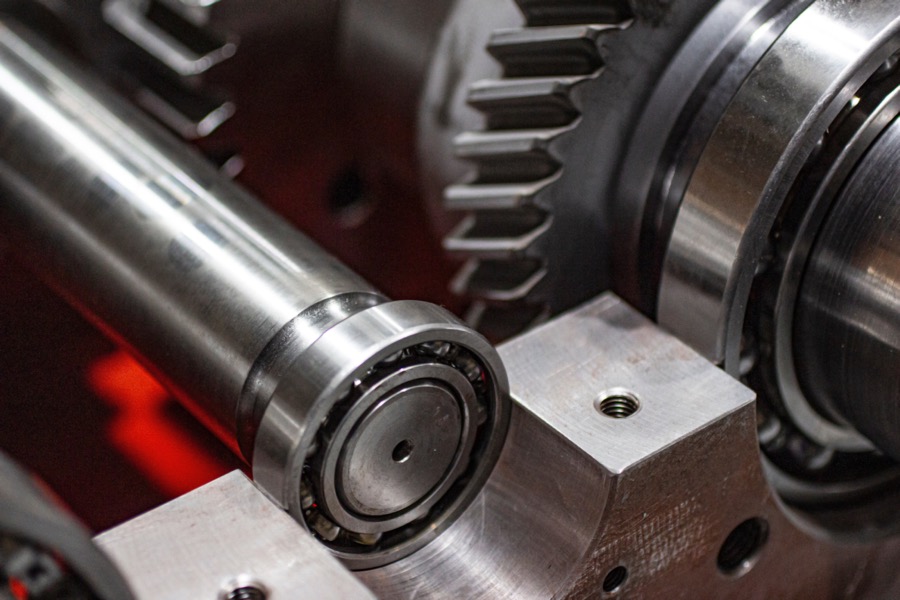
例えば、ベアリングの周りで温度が上がった形跡は無いか、軸が曲がったり振れ回っていないか、周辺部品が干渉したり偏摩耗をしていないか、オイルやグリースが異常に減っていないかなど、機構部全体を良く観察します。
「ベアリングが壊れて、ベアリングを見たら焼けていたので、新しいベアリングに変えたけどまたすぐに壊れた」
「よくよく見たら、オイル穴が詰まっていて潤滑がされていなかっただけだった」
なども可能性としては十分考えられます。
もし、ベアリング周辺の潤滑状態が良くなかったことに気がつかなければ、いくら新しいベアリングに交換したとしても、またすぐに壊れてしまいます。まさに、「木を見て森を見ず」の言葉が当てはまるかと思います。
ベアリングメーカーに調査を依頼される場合も同様に、運転状態やベアリングの周辺情報をできる限り詳細に伝えるとともに、できるだけ手を加えない状態で依頼することが重要です。
汚さないようにと気を遣って頂いて、軸やハウジングからベアリングを取り外し、ベアリング自体を綺麗に拭き上げた状態で調査依頼を頂くことがありますが、実はベアリングが取り付いていた向きや、汚れの付着状態なども調査を行う上で大きな情報です。どちらから力が加わっていたのか、スラッジなどが多い環境だったのか、ベアリング内部に侵入していた異物と外部に付着していた異物は同じかなど、様々な情報がベアリングを外したり拭き上げることで失われてしまいます。
原因を知ることはコストダウンにもつながる
「原因は良くわからないが、小さなベアリングから大きなベアリングに変えたら壊れなくなった」「原因は良くわからないが、安価なグリースから高価なグリースに変えたら壊れなくなった」
以前と比べて壊れなくなったので、ずっと同じベアリング仕様にしているという方はたくさんいらっしゃると思います。今までの実績からベアリングを選定することは、もちろん間違いではありません。ですが、コストダウンができる機会を失っている可能性があります。
例えば、大きなベアリングを用いればベアリングが負荷できる荷重というものは大きくなりますが、そもそもベアリングにそれほどの大きな荷重がかかることが、機械として正しいことでしょうか?
ベアリングに大きな荷重が発生していた真の原因が、取り付け位置がずれていたことにより発生していたアキシアル荷重だとします。その原因さえわかれば、軸やハウジングなどの加工寸法を調整して位置合わせをすることで、ベアリングに負荷される荷重は減り、小さなベアリングであっても用途に対して十分満足できる可能性があります。
他にも温度や使用環境など、ベアリングに悪影響を与えている真の原因を知ったうえで、根本の部分を対策した方がコストを抑え、かつ品質的にも安定した結果を生む場合があります。
ベアリングの故障が発生した時、その真因を探り設計品質を高められる機会が与えられているのだと思います。
名探偵を悩ませた難事件
ここまで、故障原因調査を行うことの重要性についてお話してきました。
「原因追究は行うべき」と言葉で言うのは簡単ですが、現実はそう簡単に原因追究に至るものではありません。様々な要因が複雑に絡み合って、ベアリングの故障という現象が発生している場合が多く、要因をひとつずつ紐解く必要があります。
ここで、当社の名探偵を悩ませた事件をいくつかご紹介します。
ケース1.複数個使用しているベアリングで、一部のベアリングだけ保持器が断裂する(故障したベアリングは焼き付いている様子も、剥離が起きている様子もなくスムーズに回転できる)
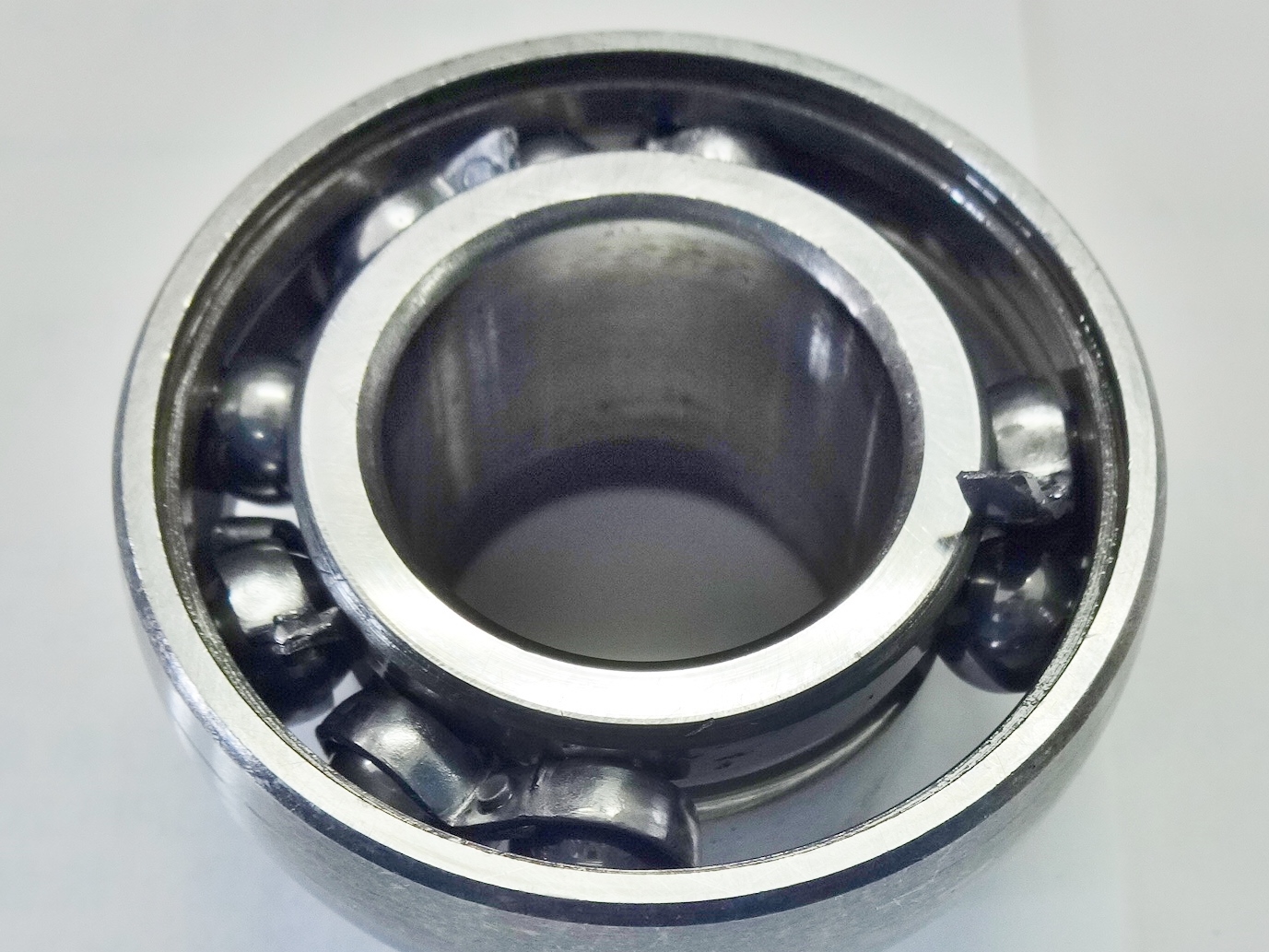

ベアリングがスムーズに回転できるのに、なぜ保持器が断裂してしまうのか?頭を悩ませてしまいました。
また、同じベアリングを複数使用しているにも関わらず、一部のベアリングだけに故障が発生し、発生する箇所もランダムという状況です。装置の詳細は不明であり、ベアリング単品状態での調査依頼であったため、ベアリング現物から痕跡を見つけるしか手段がありませんでした。
まずは同じ条件で運転し、保持器が断裂したベアリングと問題が無かったベアリングを入手し、比較調査をすることにしました。故障品も良品も外観上に傷や損傷は無く、外的な要因というのは考えにくい状態でした。
回転させた感触も特に異常は見受けられず、焼き付きや軌道面のダメージも回転感触からは判断できません。分解して内部を確認した結果も、保持器断裂に伴って発生した摩耗粉によるグリース汚れはあったものの、軌道面や鋼球に目立った傷などは発生しておらず、迷宮入り寸前です。
「保持器の初期不良」という言葉が頭をよぎりましたが、気を取り直して、軌道面の状態を良品と比較して確認したところ、転送痕と呼ばれる鋼球が転がった痕の位置に若干差があるように見えます。故障品の軌道面をもう一度、全周にわたってよく観察した所、故障品の転送痕は斜めに残っていることに気付きました。
「ん?これは、ベアリングが斜めに回っていたということではないか?」
複数あった他の故障品も確認すると、故障品は全て転送痕が斜めに、良品の転送痕はまっすぐ痕が残っていました。話として聞いたことがあったものの、当社ではこのような経験が無かったため見落としていたのですが、モーメントがかかった状態で運転されると、部分的に鋼球の公転スピードが変動することから、保持器に伸び縮みの繰り返し応力が発生し、保持器の疲労破壊に至ることがあるという知見を思い出しました。(詳しい理論は難しくなるため、省略します)
この見解を報告し、取り付け方法について見直して頂いたところ、故障の発生は収まりました。恐らく、ベアリングの取り付け時の傾きが保持器断裂の真因であったのだろうと思います。
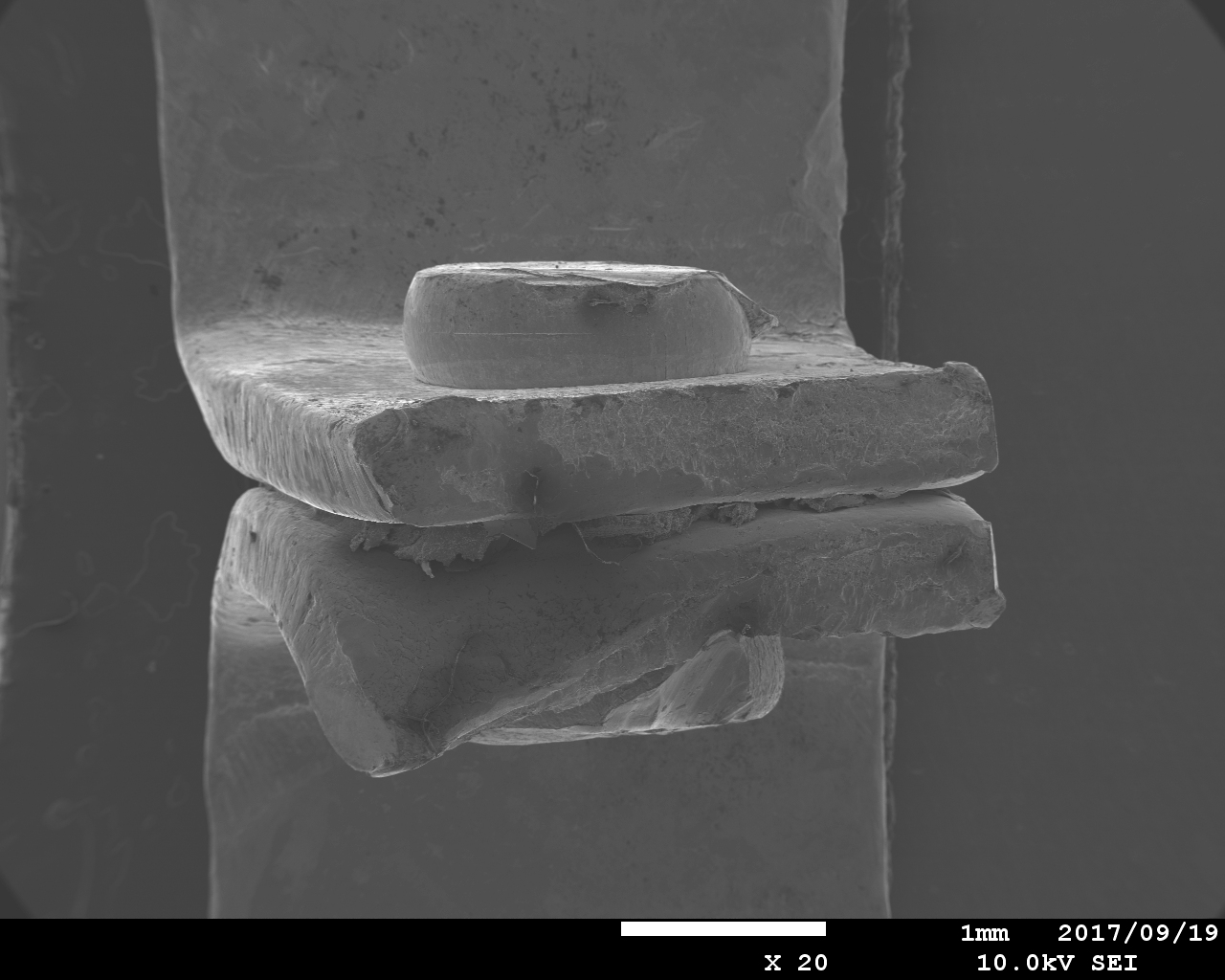
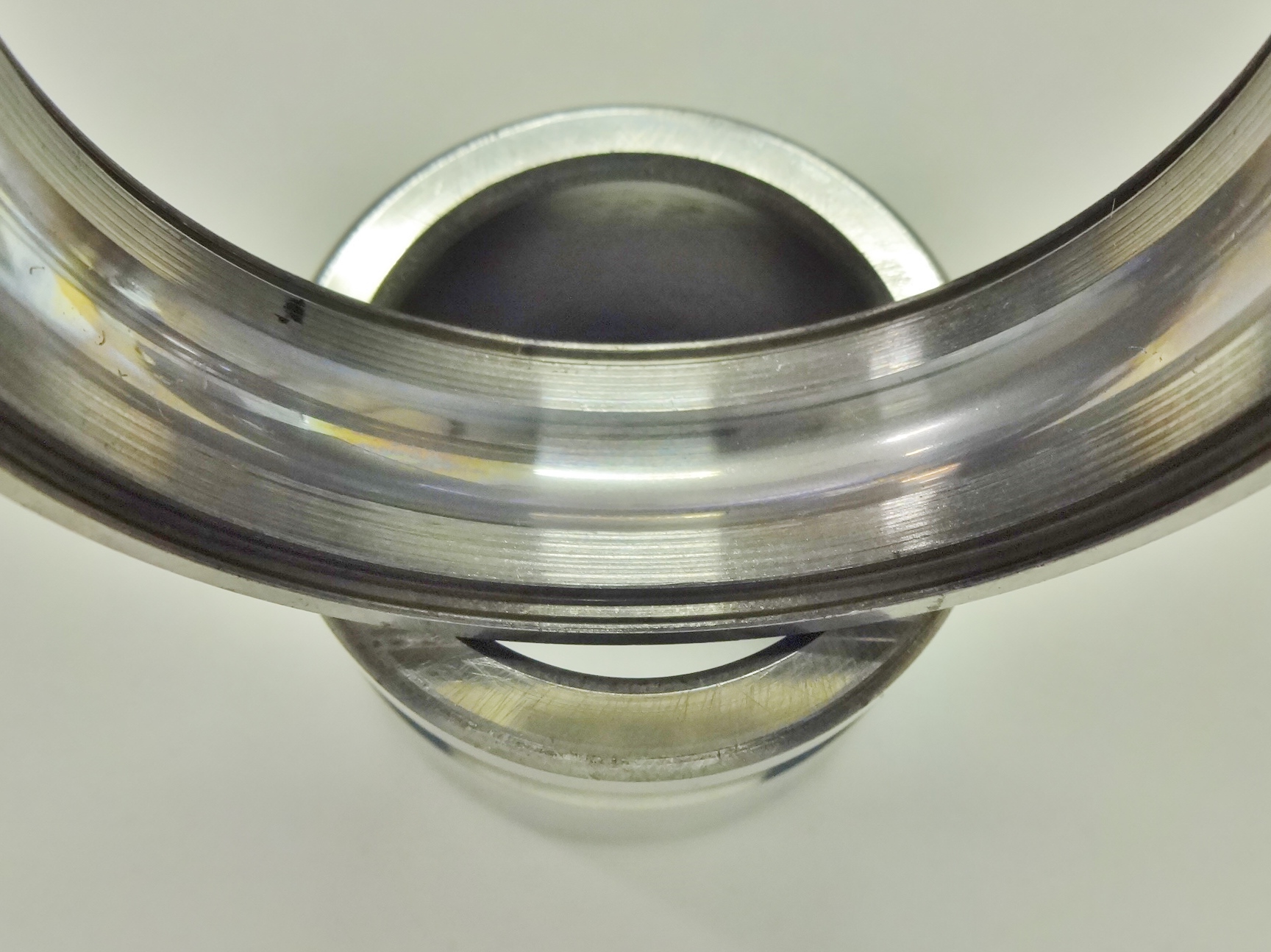
ケース2. ベアリングからグリースが漏れ出す
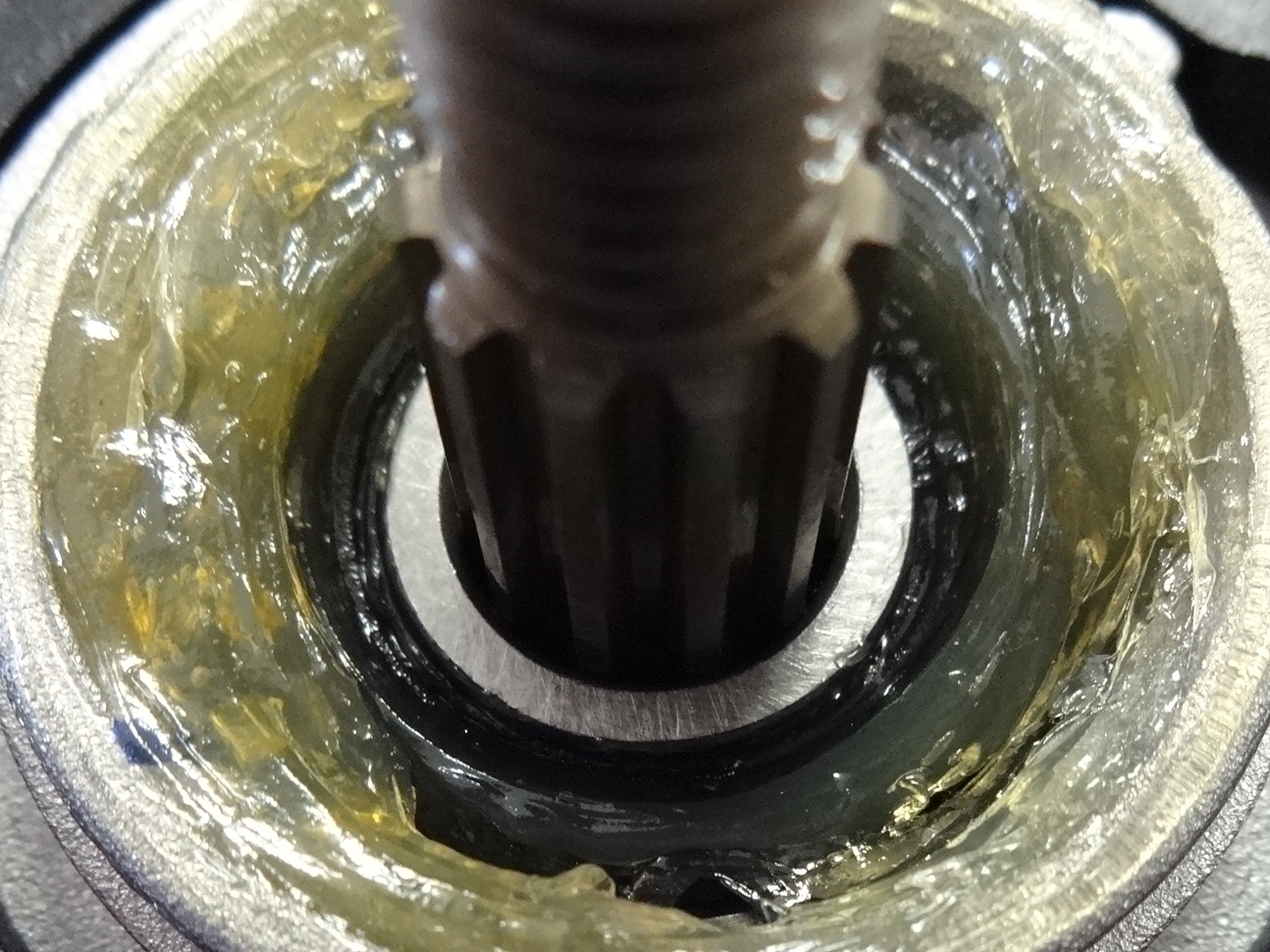
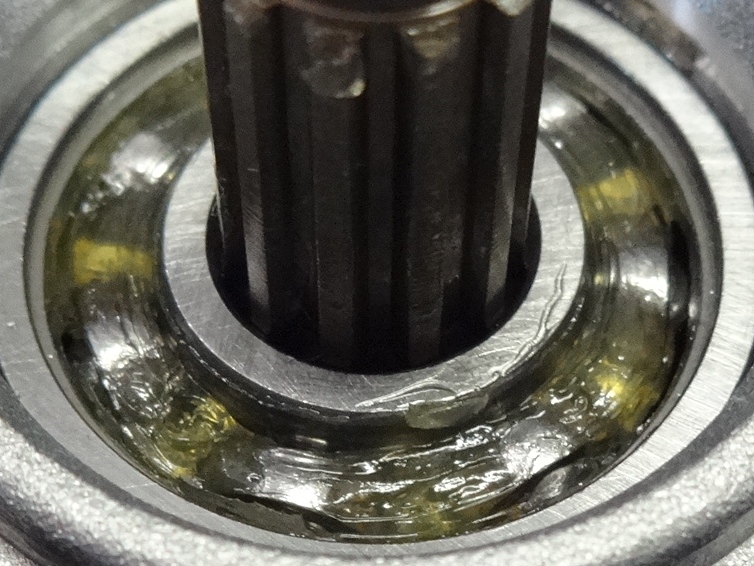
ベアリングから少量のグリースがにじみ出すことは、通常起こりうる範囲の事象ですが、初期のベアリングに封入されているグリース量より、遥かに多い量のグリースがベアリングから漏れ出ていました。
機械の運転中にベアリング内部へグリースが押し込まれていることは明らかで、ベアリングを分解すると内部にはグリースが充満していました。
このベアリングは、ギヤボックスの軸受としてご使用頂いていたようです。ギヤボックス内にはギヤを潤滑させるためのグリースを充填していたため、ギヤボックス内のグリースがベアリングに押し込まれているであろうことが想像できました。
当社より見解を報告し構造を見直していただいたところ、グリースの漏れ出しは改善されました。
不思議なのは、軸は両端2箇所のベアリングで支えており、片側は漏れ出るほどグリースが回っているのに、もう一方のベアリングにはグリースが回っておらず、焼き付き寸前です。
ギヤボックス内の内圧が上がり、ギヤボックス内のグリースが外に押し出されていることはわかるのですが、ベアリングの取り付け位置によりこれほど大きな差があることが、どうにも納得できません。温度などによる内圧上昇であれば、均等にギヤボックス内に圧がかかるはずです。
ここからはベアリングメーカーとして専門外になりますのであくまで想像ですが、ギヤボックスのギヤには、「まがりばかさ歯車」が使用されていました。
ギヤボックスの向きによる重力の影響もあるのでしょうが、要因としては歯車がスクリューのような働きをし、ギヤボックスの内部構造と合わさりグリースに圧をかけてしまったのではないかと、想像しています。
当社はギヤの設計は本業ではありませんので、歯車による流体特性の追及はせず棚上げとなりましたが、ベアリングを取り巻く環境によりベアリングに影響を与えることがある好事例となりました。
ケース3. ゴムシールがめくれ上がっている
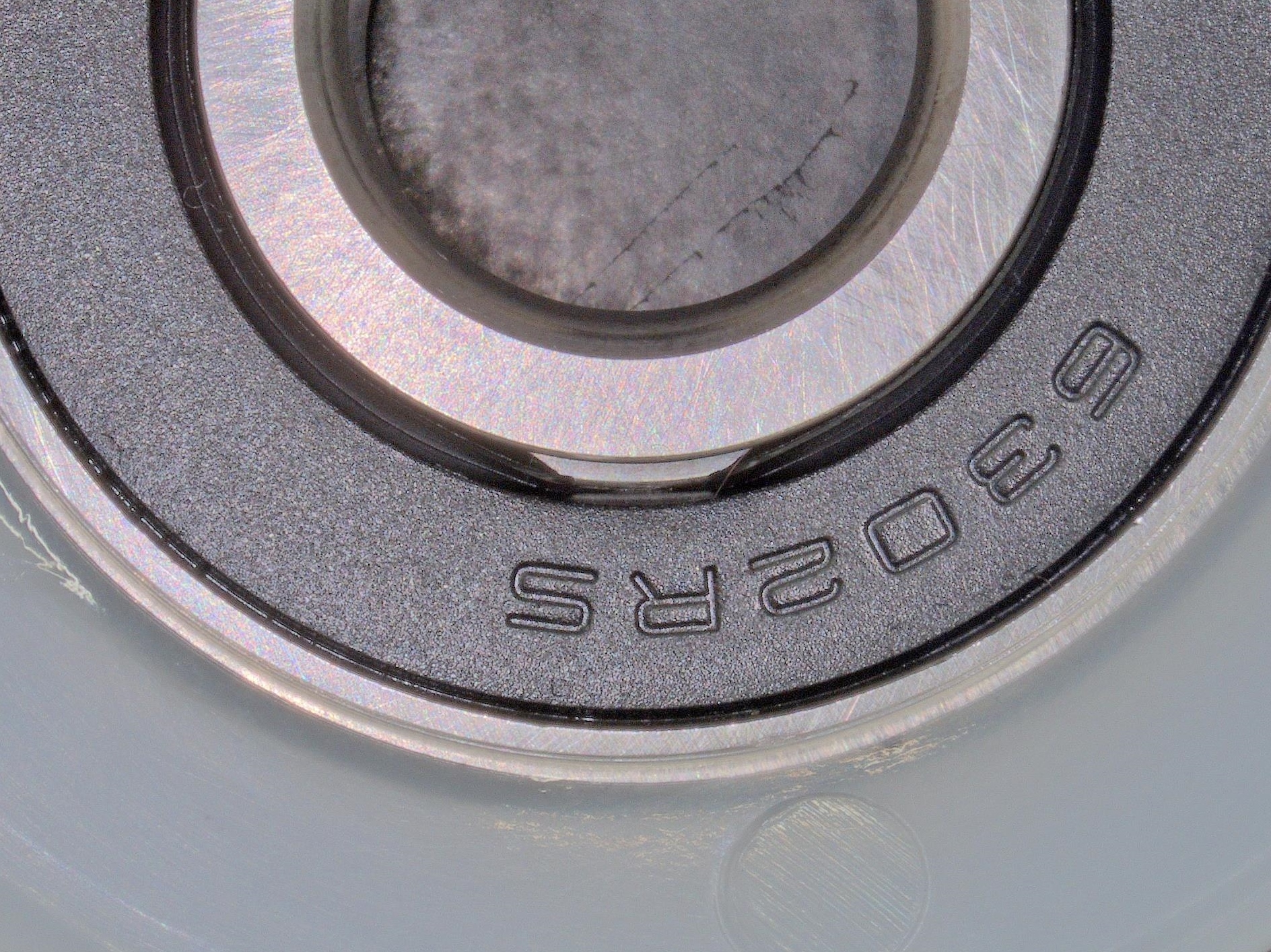
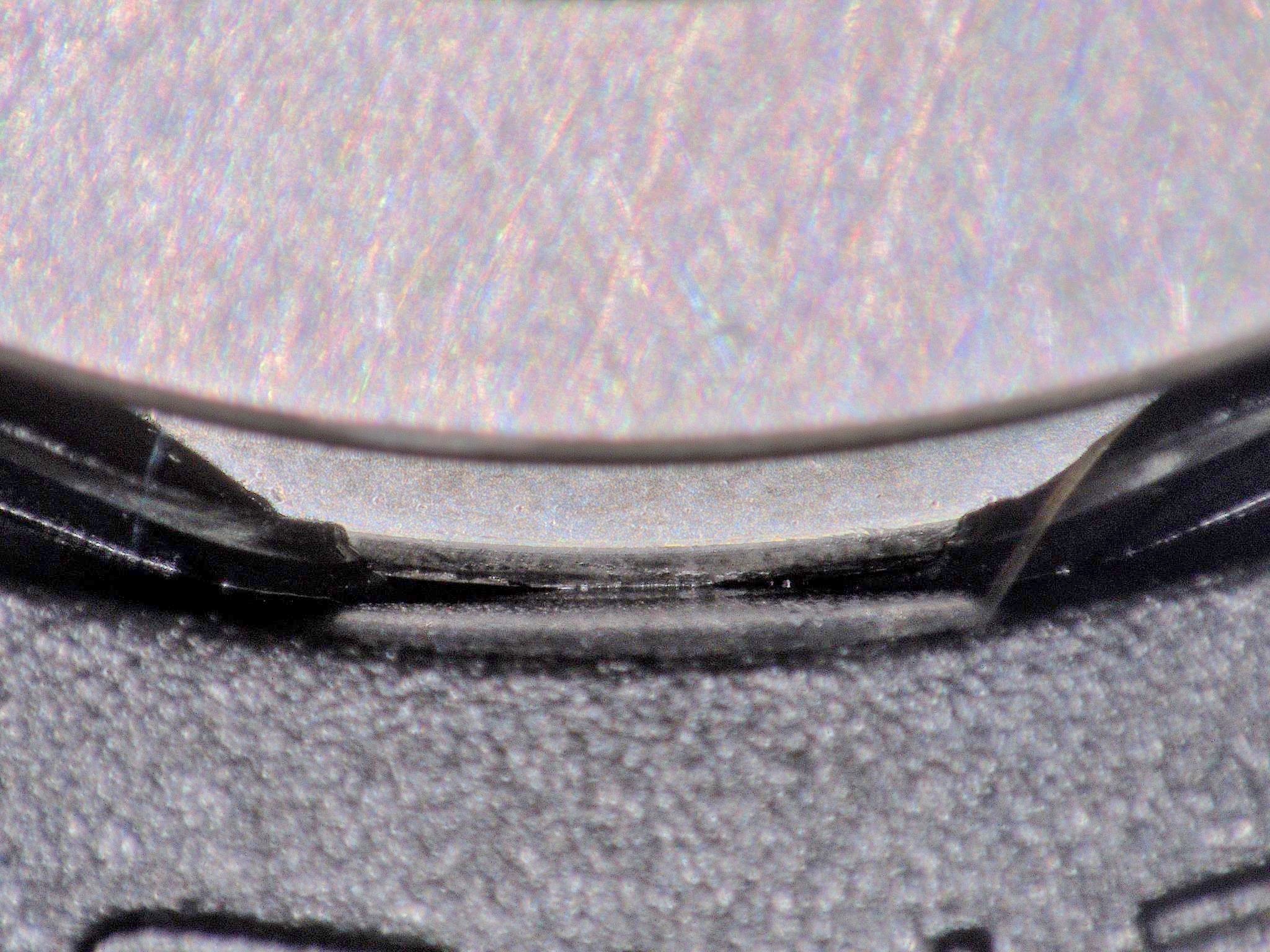
「新品のベアリングで、ゴムシールの接触部分がめくれ上がっているものが大量に発生している」ということで、ベアリングの初期不良を疑われ調査を行うことになりました。
当社で全数目視検査を行っていた製品であり、検査見落としの可能性はあるものの、発生数量から考えると検査時点での見落としは考えにくい状況でした。当社側で考えられる要因として、検査工程自体を飛ばしてしまったことが考えられましたが、検査履歴が残っており工程を飛ばしたことは考えられません。
調査依頼のあったベアリングの現品を確認すると、外輪に樹脂が成型されていました。当初のお話にはありませんでしたが、調査にあたり詳しくお尋ねしたところ、お客様にてベアリングへ樹脂成型を行って、最終製品にしていたことが判明しました。
この成型工程で、何かしらの現象が発生している可能性が高いように思い、成型工程を調査することにしました。
樹脂を成型するには、金型を使って密閉された所へ樹脂を押し込んで固めます。この時、金型の合わせ面から樹脂が漏れ出るとバリとなって製品に影響しますので、金型を精度よく合わせて、圧をかけて金型を密閉させます。
ここで考える必要があるのは、樹脂が漏れないように密閉するということは、空気も漏れにくい構造であるということです。
樹脂を注入するときに金型内に空気があると、うまく樹脂が流れませんので空気を抜くための穴が設けられます。樹脂が充填される部分はそれで良いのですが、ベアリングがセットされる部分の空気はどうでしょうか?
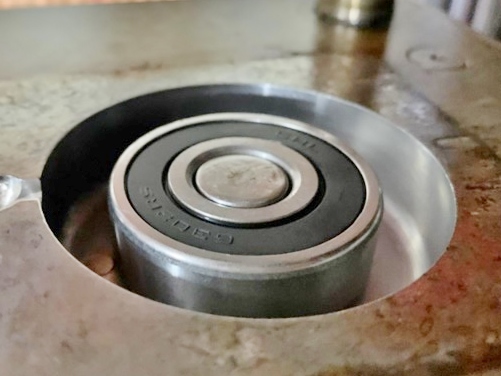
ベアリングはシールで密閉されているので、ベアリング内部は大気圧のままです。ベアリングがセットされる部分にも適切な空気抜きが無いと、圧がかかった場合に空気はシールを押して、ベアリングの内部へ流れ込もうとします。この時に、ゴムシールをめくれ上がらせてしまうのです。
金型を確認した所、ベアリングセット部の空気を抜く考え方がありませんでした。恐らく、金型を締めた後に樹脂を流し込む事で温度上昇により膨張した空気の逃げ場が無くなり、ゴムシールを押してしまっている事で発生しているであろう見解を報告し、金型の空気穴を適切に配置してもらった所、ゴムシールのめくれ上がり現象は発生しなくなりました。
故障の原因を知って新たなステージへ
先にも書きましたが、故障の真の原因を知ることは、製品開発にとって大きなメリットになることがあります。コストメリットだけではなく、新しい着想により優れた機構が生まれるチャンスでもあります。
しかしながら、真の原因にたどり着く作業は手間も時間もかかるため、人の思考は単純な解決方法へ向かいがちになってしまいます。また、調査を行うには積み重ねてきた経験・知見がないと、現象を推定することが難しい場合もあります。
当社ではこれまで蓄積してきたノウハウを基に、お客様のベアリング調査のお手伝いを通じて、お客様のより良い製品開発のサポートをさせていただきます。