ベアリングの故障とは?
「形あるものはいつか壊れる」と言いますが、ベアリングはいつか必ず壊れます。
ベアリングの運転を開始して壊れるまでの時間を「寿命時間」として定義します。この寿命に至るまでの時間が想定よりも早ければ異常(故障)、想定通りであれば正常、というように判断は変わります。
例えば、鉛筆は書いているうちに芯が減り、いずれ書けなくなってしまいますが、これは正常な状態と言えます。一方で、まだまだ書くことができる鉛筆の芯がポキポキと折れて書けなくなってしまうのは、異常な状態と言えます。
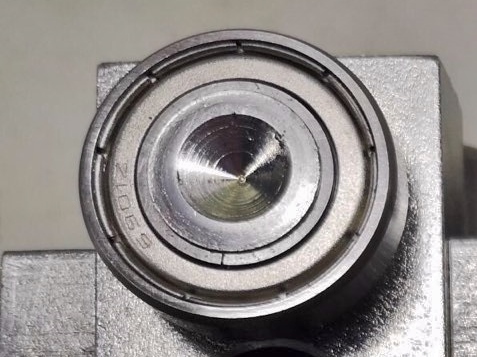
ベアリングも同じです。想定された寿命を迎えて壊れてしまう現象は正常な状態であると言えますが、想定された寿命よりも早期に壊れてしまうことを「ベアリングの故障」として定義しています。(寿命のお話は、またの機会に別コラムでお話いたします)
では、ベアリングが故障する原因にはどのようなものがあるのでしょうか?
ベアリングの故障と言うと、一般的には“フレーキング(剥離)”“焼き付き”“クリープ”などが紹介される場合が多いですが、実はこれらは故障の「原因」ではありません。“フレーキング(剥離)”“焼き付き”“クリープ”などは故障時に発現した「現象」になります。故障の原因は、この現象が発生する前段階の事象になります。
故障の原因について
では、故障の原因はどこにあるのでしょうか?
ベアリングが世に誕生してから積み重ねられてきた知見により、軸受の状態(故障時に発現した現象)から、原因はある程度推察することができます。
故障時に発現した現象 | 現象の状態による分類 | 推察される主な原因 | 主な対策 |
---|---|---|---|
フレーキング
|
軌道の中心からずれた位置に発生 (深溝玉軸受の場合) |
|
|
円周方向の対称位置に発生 |
|
|
|
早期に発生 |
|
|
|
軌道に転動体ピッチ間隔で発生 |
|
|
|
発生箇所に規則性がない |
|
|
|
すりきず・かじり |
|
|
|
割れ・欠け |
外輪・内輪・転動体に発生 |
|
|
保持器に発生 |
|
|
|
焼付き |
|
|
|
圧こん |
転動体ピッチ間隔で発生 <ブリネリング> |
|
|
ランダムに微小な痕が発生 |
|
|
|
錆・腐食 |
ベアリング内部に発生 |
|
|
はめあい面に発生 |
|
|
|
ベアリング表面に発生 |
|
|
|
スミアリング
|
|
|
|
なし地
|
|
|
|
変色 |
|
|
|
異常摩耗 |
転動体ピッチ間隔で軌道面に発生 <フォールスブリネリング> |
|
|
はめあい面に赤褐色状の摩耗粉を伴う 摩耗が局部的に発生 <フレッチング> |
|
|
|
軌道面・転動体表面・保持器などに発生 |
|
|
|
内径又は外径面に鏡面、かじり傷が発生 (クリープ) |
|
|
|
電食 |
|
|
ベアリング故障のほとんどは未然に防げる
当社の経験してきたベアリングの故障のほとんどは、ベアリングの取り扱いの誤りから発生している故障が大部分を占めます。
ベアリングは非常に精密に作られた機械部品ですが、見た目からは精密さが伝わりづらく、他の機械部品と同じ様に扱われてしまうことが多くあります。
例えば、注射針のように細いピンをハンマーで叩き込んだりする人はいません。
これは、感覚的・視覚的にそのような扱いをしたら壊れることを経験上知っているからです。
実は、ベアリングは注射針の太さの10分の1から100分の1のオーダーで寸法管理をしている部品になります。乱暴に扱ったり、扱い方を間違えると、精密に管理している寸法もその意味が無くなってしまいます。
ベアリングという部品を良く知り、正しい使い方をすることが、ベアリングが持つパフォーマンスを最大限に引き出すコツと言えます。
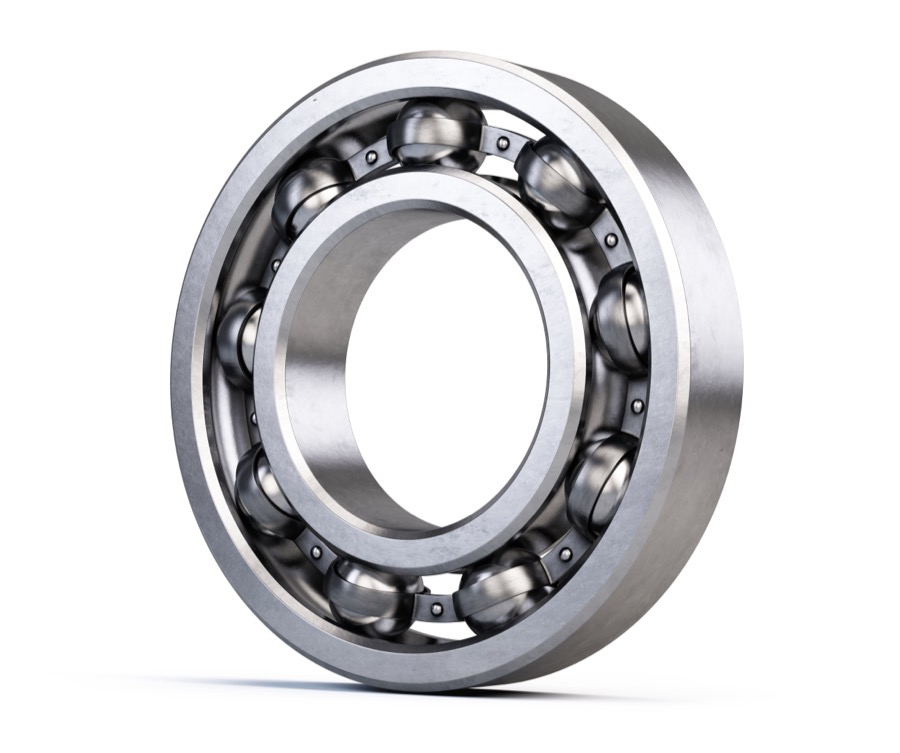
ベアリングを扱う上で注意すべきポイント
今回は当社の経験上、多く見られる現象から代表的な注意ポイントをピックアップさせていただきます。
ごみ・錆・衝撃はベアリング故障の主要因
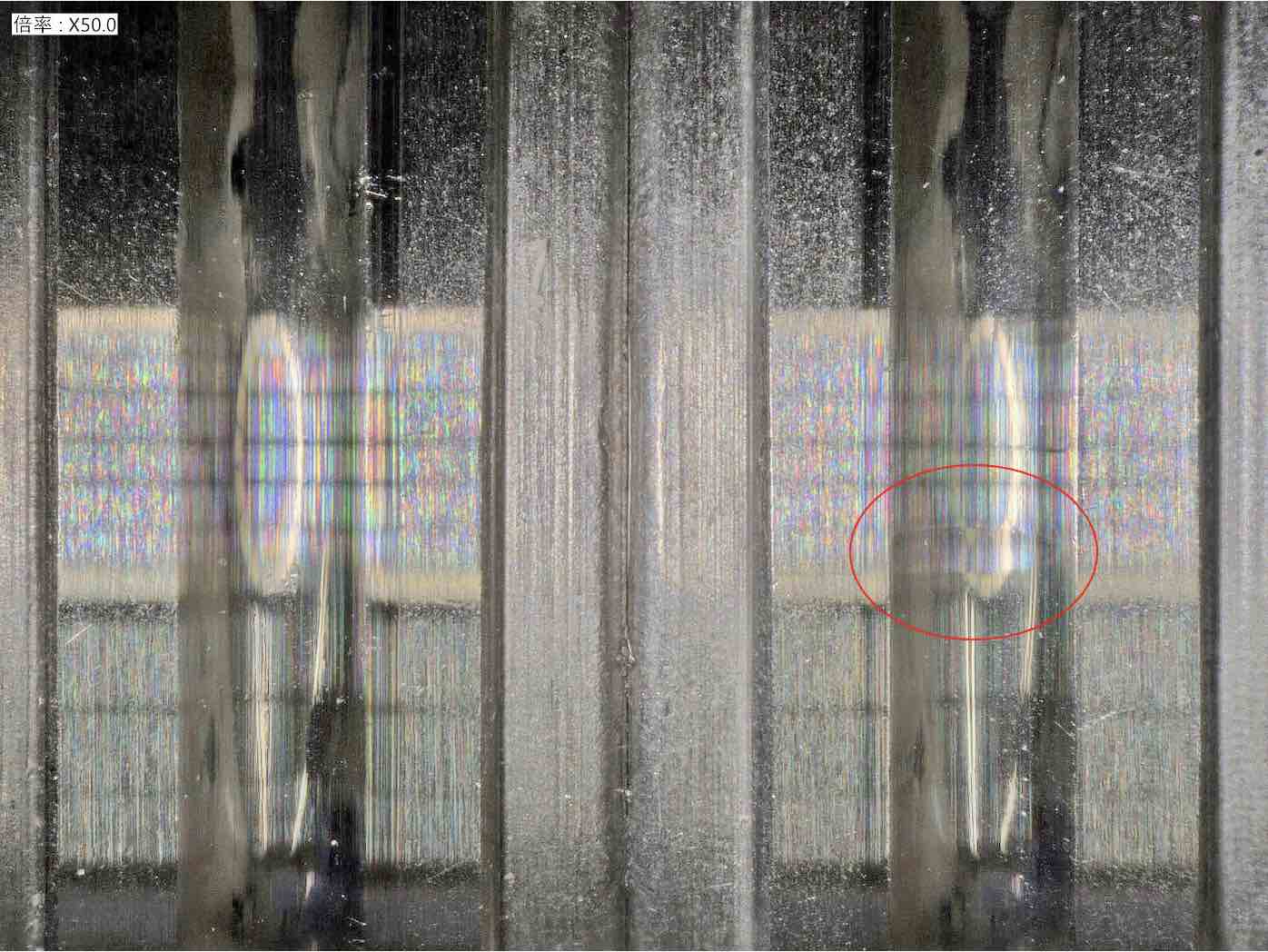
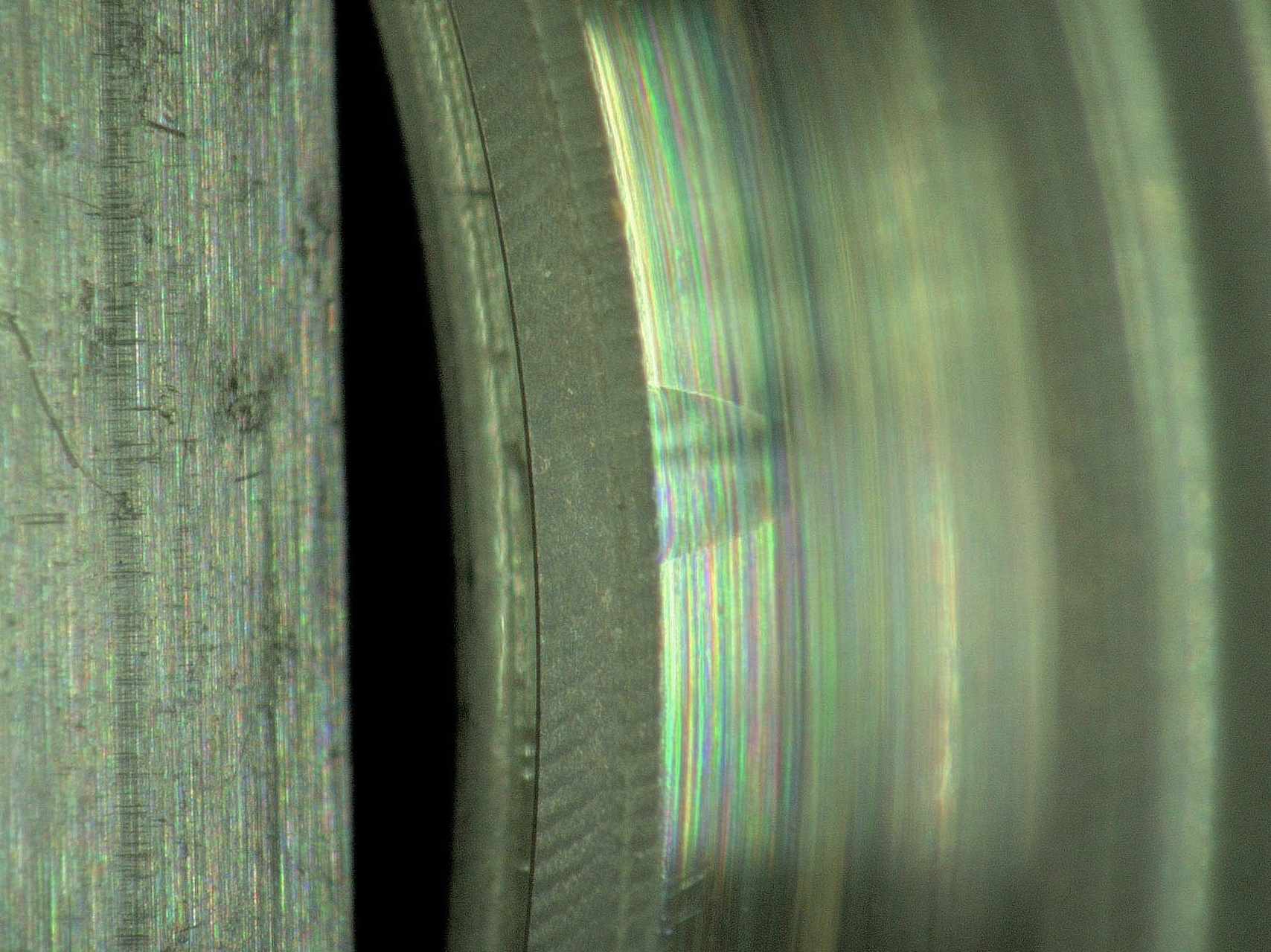
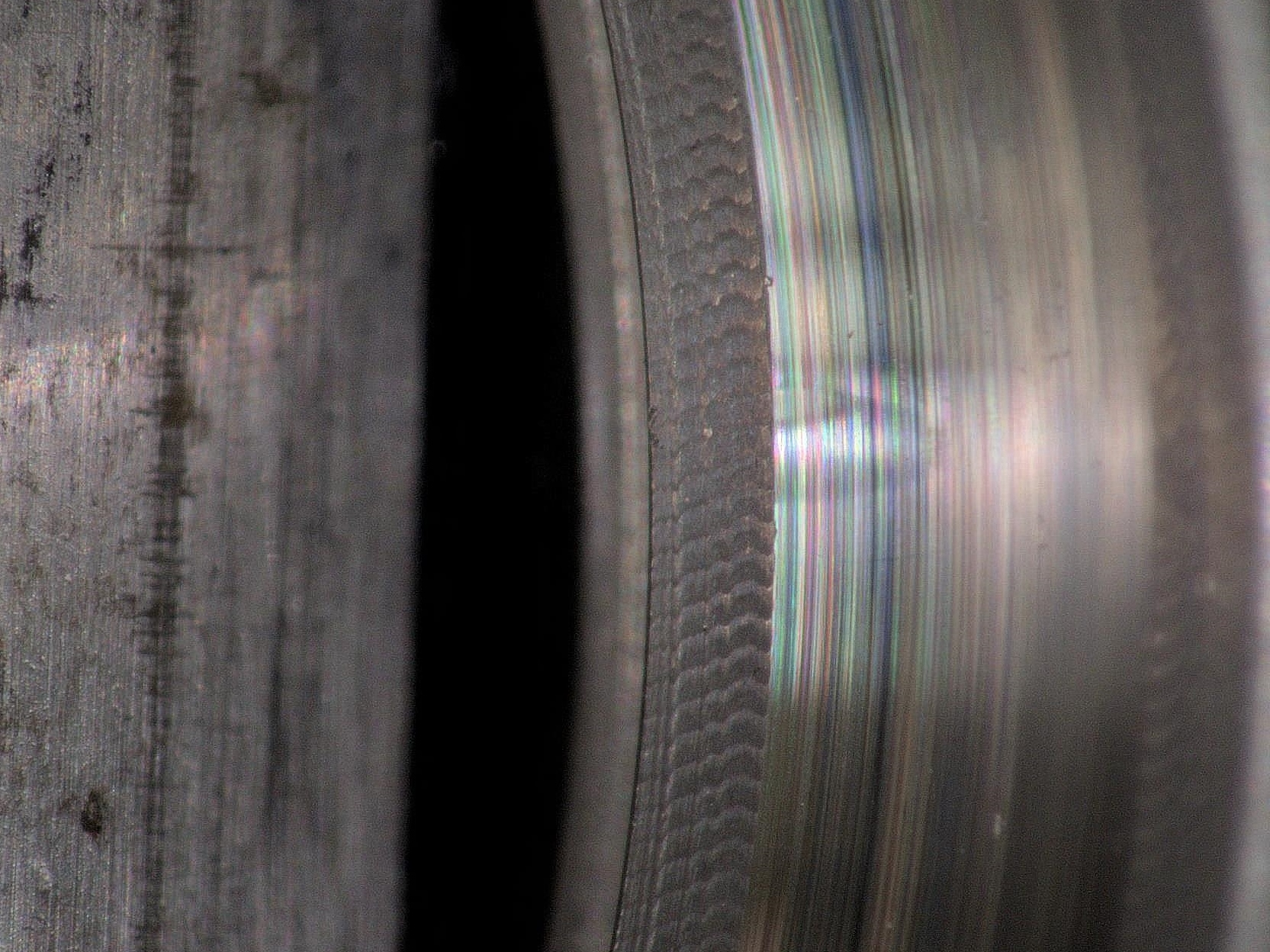
故障のなかでも多く発生する事例として、衝撃による圧痕が発生したことによる故障です。
ベアリングは何かに取り付けられて使われることがほとんどですが、注意すべきポイントは「取り付ける」という行為です。
取り付けはハンマーで打ち込んだり、プレス機で圧入して取り付ける場合が多いですが、扱いを間違えて組み付けてしまうと、ベアリングは簡単に壊れてしまいます。ボールベアリングは一見鉄の塊に見えるため、見た目からは想像しにくいですがベアリングの内部は点と点で支えている非常に繊細な構造となっています。
点と点で支えているからこそ、なめらかな回転運動ができるのです。これが面と面だと、摩擦が大きくなってなめらかな回転にはなりません。
点で力を加えるということについて、画鋲を壁に刺す行為を想像してみてください。画鋲を壁に刺すと、針の方が壁に押し込まれていきます。
しかし、画鋲の頭が壁に刺さった針と同じ分だけ指に押し込まれてくることはありません。これは、針が点、頭が面であることにより、そこに発生している力が異なるからです。
専門的に言うと、「面圧」と言う言葉を使います。
もし、画鋲の頭が無くて両側が針だったら、針は指に刺さってしまいますね。
ベアリングの内部でも同じことが起こっています。
ハンマーで叩いた場合、見た目は何ともなくとも、内部の点で支えている部分に力が加われば、その部分は簡単に凹んでしまいます。
この凹み痕のことを「圧痕」と呼びますが、当社の過去の経験からも多くの圧痕発生事例を見てきました。
これはベアリングの構造をよく理解せずに扱ったことで発生する、典型的な事例となります。
圧痕を発生させてしまったことによりベアリングの回転感触がゴロゴロする、運転時に異音がする、最悪の場合は圧痕に応力が集中することで、その部分から剥離が発生しベアリングが壊れてしまいます。
ハンマーで打ち込んだり、プレス機で圧入するという取り付け方法そのものは否定しませんが、荷重をかけて良い部分、駄目な部分を間違えてしまうと、あっという間にベアリングを壊してしまいます。
圧入の程度を知らないと故障の原因となる
ボールベアリングを取り付ける際に、小さめの穴や大きめの軸にベアリングを打ち込んで固定する方法を取ることがあります。
この方法を「圧入」による取り付けと呼びます。「圧入」は容易に取り付けが可能であるため、多くの場面で用いられる方法ですが、設計上有効な反面適切な設計や精度管理を行わないと、ベアリングを破損させるリスクが多く含まれています。
先ほどもお話した通り、ベアリングは一見鉄の塊に見えますので丈夫なように見えますが、いくら高強度の鉄であっても、その厚みによっては簡単に変形したり、割れたりしてしまいます。
わかりやすく例えると1円玉を指で曲げることは難しいですが、アルミホイルであれば指で簡単に曲げることができると思います。
圧入によりベアリングは少なからず変形します。
薄肉のベアリングの場合だと、手で押しただけでも数ミクロンの寸法変化をさせることができます。
ボールベアリングには、スムーズに回転できるように軌道と鋼球の間にミクロンレベルのすきまを設けていますが、変形によってすきまが無くなると、回転感触がとたんにゴロゴロし、抵抗がある感じに変わります。この状態で無理に運転させると、異音や焼き付きなどを発生させてしまう可能性が高まります。
変形の許容量を超えて変形させてしまうと、ベアリングにクラック(割れ)が発生してしまうこともあります。圧入していないから大丈夫と考えていても、結果的に圧入と同じ状態になってしまっていることもよくあります。軸にベアリングを取り付けた後で、カシメを行って固定する場合など、カシメによって軸が膨らんで(太くなって)しまいベアリング内輪にクラックを発生させてしまう事例も多く見られます。
リブ形状の部品に圧入する場合なども要注意です。リブのある部分と無い部分で変形量が異なるため、折角真円に加工されたベアリングがいびつな形状になり回転に悪影響を与える場合があります。
逆に、圧入が弱すぎることも問題です。
ベアリングが十分固定されずに動いてしまうことで、圧入部が摩耗してしまったり、発熱したりする原因となります。
ベアリングの構造を良く知り、適切な固定を行うことが故障を回避するポイントとなります。
取り扱いによる故障を未然に防ぐには
既にお話させて頂きましたが、近年ではベアリングの加工技術、材料の進化も進み、ベアリングの初期不良による故障事例は非常に少なくなってきています。
発生する故障は、取り扱いの間違いに起因する場合がほとんどです。
ベアリングの構造を良く知った上で、適切な取り扱いを行うことが故障を未然に防ぐ重要なポイントとなります。
ただし、これはベアリングメーカーにすべて任せて解決できる問題ではありません。
ベアリングメーカーでは千差万別であるお客様の使用方法や取り付ける部位の構造、取り付け方法などを知りません。
その情報は、お客様しか知りえない情報だからです。
機密につき情報が開示できないという理由はよく理解できますが、ことベアリングに関してはベアリングメーカーと2人3脚で進めないと、故障を多発させてしまう原因となりかねません。
当社に詳しい情報を開示頂ければ、ベアリングの構造を良く知る技術者により、お客様の用途に合わせたベアリングの選定や設計上のアドバイス、取り扱いのサポートをさせて頂くことが可能です。